提高五軸數(shù)控磨床的效率需要從設(shè)備優(yōu)化、工藝改進、編程策略、自動化集成以及人員培訓(xùn)等多個方面入手。以下是具體的方法和策略:
一、設(shè)備優(yōu)化與維護
1.提升設(shè)備性能
選用高性能主軸和伺服系統(tǒng):提高轉(zhuǎn)速和響應(yīng)速度,縮短加工時間。
優(yōu)化機床剛性:增強機床結(jié)構(gòu)穩(wěn)定性,減少振動和變形,確保高精度加工。
升級控制系統(tǒng):采用先進的數(shù)控系統(tǒng)(如西門子、發(fā)那科等),支持多軸聯(lián)動和高速運算。
2.定期維護與校準
保持設(shè)備精度:定期檢查和維護導(dǎo)軌、絲杠、主軸等關(guān)鍵部件,防止磨損影響加工效率。
校準刀具和夾具:確保刀具鋒利度和夾具定位精度,減少因誤差導(dǎo)致的返工或報廢。
1.優(yōu)化磨削參數(shù)
調(diào)整切削速度、進給量和磨削深度:根據(jù)材料特性(如硬度、韌性)選擇最佳參數(shù),避免過切或欠切。
采用高效磨料:使用CBN(立方氮化硼)或金剛石砂輪,提高磨削效率和壽命。
冷卻液管理:優(yōu)化冷卻液流量和溫度,減少熱變形并延長砂輪壽命。
2.減少非加工時間
縮短裝夾時間:使用快速裝夾系統(tǒng)(如氣動夾具、真空吸盤)或自動化上下料裝置。
合并加工步驟:通過五軸聯(lián)動功能,在一次裝夾中完成多個面的磨削,減少裝夾次數(shù)。
3.優(yōu)化加工路徑
減少空行程:規(guī)劃最短的刀具移動路徑,避免不必要的機床運動。
分層加工:對復(fù)雜曲面采用分層磨削,逐步逼近最終形狀,提高加工效率。
三、五軸數(shù)控磨床編程與仿真
1.高效數(shù)控編程
使用專業(yè)CAM軟件:如Mastercam、HyperMill等,自動生成優(yōu)化的五軸加工路徑。
參數(shù)化編程:將常用工藝參數(shù)標準化,減少重復(fù)設(shè)置時間。
宏程序應(yīng)用:利用數(shù)控系統(tǒng)的宏功能,實現(xiàn)復(fù)雜邏輯的自動化控制。
2.虛擬仿真與驗證
加工前仿真:通過仿真軟件檢查刀具路徑和碰撞風(fēng)險,避免實際加工中的錯誤。
優(yōu)化刀具軌跡:在仿真中調(diào)整路徑,減少冗余運動,提高加工效率。
四、五軸數(shù)控磨床自動化與智能化
1.自動化上下料
集成機器人:配備工業(yè)機器人(如六軸機械手)實現(xiàn)自動上下料,減少人工干預(yù)。
自動化料倉:使用自動換料系統(tǒng),實現(xiàn)連續(xù)加工,減少停機時間。
2.智能監(jiān)控與優(yōu)化
實時監(jiān)測:通過傳感器監(jiān)測加工狀態(tài)(如功率、振動、溫度),及時調(diào)整參數(shù)。
數(shù)據(jù)分析與優(yōu)化:利用工業(yè)大數(shù)據(jù)和AI技術(shù),分析歷史數(shù)據(jù),優(yōu)化加工參數(shù)和路徑。
3.遠程運維
物聯(lián)網(wǎng)(IoT)集成:通過遠程監(jiān)控平臺實時查看設(shè)備狀態(tài),提前預(yù)警故障,減少停機時間。
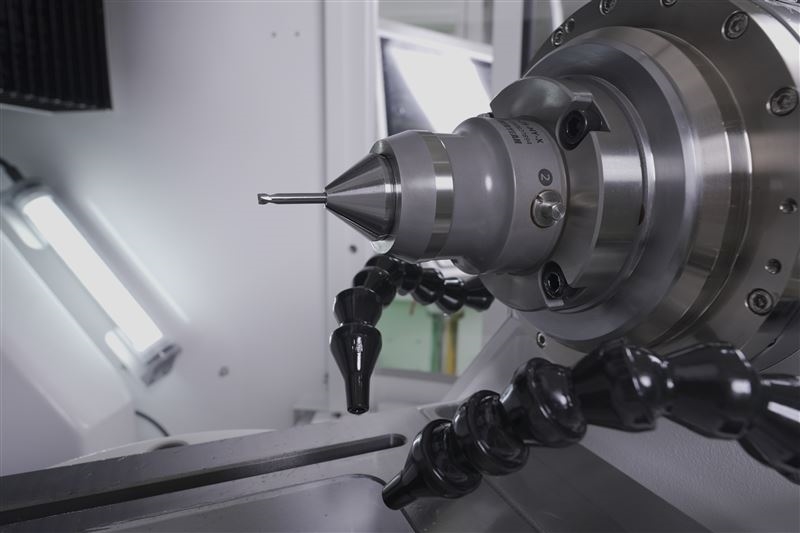